Shuttering works
Shuttering Work in Construction
Objective
The objective of Shuttering work method statement is to erect all types of formwork (here we explained for columns and walls) meeting the technical Specification and confirming with IS Standards.
Scope
The scope of shuttering work in construction includes the method statement, starting from Inspection of proper material, erection and removal of formwork, at project site while executing it in accordance with IS standards and BOQ specifications.
Reference
“Good for Construction” Formwork drawing
Tools Used
Right angle, Line thread, Tube level, Hammer, Hand saw, Spirit level 2-3 m, Plumb bob, Total station, Shuttering tape, Measuring tape, Chipping tools and Pinch bar.
Materials Used
Ply wood, Props, Cup locks, Base plates, U – heads, Runners, MS square tubes, Hollow Section, C – clamps, Acro – spans, Bracing pipe and Swivel couplers, Shuttering oil, Poly foam, runners, purlins, reapers, Tie rods, U clamps.
Procedure
The centring and Shuttering System consists of Plywood as sheathing material, Steel Whalers (horizontal members used for shuttering support) as primary members and H beams as secondary members. The Alignment of shuttering to be done by adjusting upward and downward movement by Telescopic props.
Shuttering work :
- Making of shutter panels straight and right angles to each other using right angles as per approved formwork drawings.
- It is important that all the staging materials should be visually checked and confirmed its sturdiness before being used at site.
- Formwork shall be erected in such a way that, it should support safely the worst combination factors of all Loads within prescribed tolerance limits and not causing any bulging or Deflection over concrete.
- Always remember that, while doing slab shuttering work,the staging should rest on solid ground or over ISMB sections anchored well to the Concrete structure (I strongly recommend PCC floor) below. Base plates should not be placed on bricks or solid blocks which are likely to get crushed when wet.
- Ply wood material used for shuttering, should be dimensionally accurate in length, width for slabs and in depth for beams and also give the desired finish to the contact surface. Always, it is advisable to go for waterproofing plywood boards.
- Staging shall be true, rigid and thoroughly braced, shuttered and propped.
- To achieve desired rigidity, adequate bracing is to be provided. In case of cup lock shuttering system, bracing is automatic.
- The purpose of application of formwork oil to the shuttering surfaces is to create a separate medium between concrete and shuttering. It also helps keep the formwork clean and gives extra life to the shuttering in terms of more repetitions. The formwork oil to be applied 48 hours prior to concrete in case of roof concreting, and 2 – 3 hours in case of columns and wall concreting by foam gently smeared in oil.
- It is recommended to use a Branded shuttering oil or mixture of Grease and Diesel. Burnt machine oil or used oil is strictly not to be used, which is unsuitable and not only spoils shuttering surface, also have effects on concrete surface against plastering.
- Camber : For all spans in excess of 5 meters for beams and slabs, it is highly advisable to give a camber of 2 mm per 1 meter. Similarly for Cantilever portions, a camber at the end of span of 4 mm per 1 meter is recommended.
- Always for safety point of view, at all surfaces including even and slope surface, the erection of casing and shifting of formwork shall be effectively carried out under the personnel supervision of experience shuttering foreman.
- As per IS 456:2000, the Striking time for formwork or de-shuttering works, under normal conditions is as follows.
- In case due to weather conditions if the concrete is taking extra time for its setting, the de –shuttering time to be extended after discussing with the project manager.
Caution: Before removal of formwork it is highly recommended to obtain the 7th day cube test results for slab, beams and staircase.
- Formwork is designed and constructed to the required dimensions, lines and shapes, shown on the drawings with the tolerances given below.
- Tolerance for cross-sectional dimensions of cast in-situ: +10 mm / -5 mm.
- For cast in-situ elements, the deviation of level of any point from the intended level: ± 10 mm.
- Tolerance for plumb: 3 mm / m, maximum 20 mm.
- Place the Shutter panel (fabricated with H-16 beams, Plywood’s and Steel Whalers) on all four sides for walls or columns and check the line and level.
- Continue the fixing of Shutter panels, with level and alignment checking till the end on one side of the wall.
- After one side of shutter fixing Fix cover blocks at 600 c/c on both sides.
- Similarly fix other side shutter panels and check the line &level, then place remaining shutter panels continuously.
- Place the alignment props at required places with head/foot adapter assembly.
- To maintain uniform wall thickness, fix the Timber spacers at regular intervals of every 1 m distance the top between the shutter panels.
- Use alignment struts for checking plumb for shutters and double check with plumb bobs.
- The alignment of shutters on both sides can be checked and fixed with the help of fixing line thread on top of the plywood boards.
- To checking inside corners of shuttering, Use inside right angle corners and tighten the supports to match the requirements on the outer side boards.
- Use separate and independent cup-lock scaffolding with platforms for concrete personnel.
- Concrete to be filled in layers of 300 mm height and up to 900 mm ht. per hour to restrict the designed concrete pressure.
- Caution: concrete pipe line should not be connected or supported to shutters. Always use independent vertical support staging system for pipe line.
Remove the wing nut first, then, Alignment Struts and Accessories. Tie rods used for shuttering, shall be sacrificed and cut 25 mm inside the surface.
Remove shutters one by one.
Construction Manager: should take responsible for all construction activities.
Site Engineer: should take responsibility for executing all work in safe manner as per drawings. He shall guide the foremen and work men in the execution of work.
Site Supervisor: Responsible for managing all plant and machinery and men including the safety of workers.
QA/QC In charge: Responsible for ensuring the quality of work as per the standards and specifications.
HSE Manager/Engineer: Maintaining safety standards at project site is paramount important, and it is the responsibility of HSE manager to giving proper instructions to all supervisors, engineers to ensure the safety of workers during the progress of work. Safety inductions of each staff including new comers and workers shall be done. Daily PPE checks to be done and tool box talk at the morning hours before the start of work.
Safety compliance required for the activity: to be enforce at site
Connect with us to avail a complete construction services
Shuttering Works- Formwork
Formwork is a shape or mould comprising all supporting arrangements, used to outline and backing the concrete until it attains adequate strength to carry its self-weight. It shall accomplished to carrying all compulsory dead load and live load including its self – weight.
1. Requirements of Good Formwork
- PCC floor : Always the formwork should rest on solid, hard and firm base. E.g. on PCC floor over well compacted soil.
- It should firmly erected, well propped, supported and to retain its structure with proper horizontal and vertical bracers.
- As already told, it should accomplished to carrying all compulsory dead load and live load.
- Water tight : All joints of shuttering work should be water tight against possible leakage of concrete slurry.
- It is always recommended that, the cost of shuttering work not only to minimum and at the same time to maintain the consistent safety.
- Materials used : The material used for the shuttering work should be economical, easily available and to produce maximum repetitions after its reuse.
- Design and making of shuttering should permit stripping of all components in preferred sequences without damage to the concrete surface.
- The quality and method of formwork is designed in such a way that, it should satisfy the required dimensions, shape, level and finish of the concrete obtained.
- The internal surface of this work, should always maintained with smooth surface by applying branded shuttering oil, so that the stripping of formwork will be easy and also good concrete surface finishing can be expected.
- Shuttering work should be as light as possible and the material used should not warp or get distorted when exposed to the atmospheric elements.
2. Cost of formwork
- The cost is approximately between 30 – 40% of the cost of concrete work in case of regular structural work
- In case of Special infrastructures like Flyovers, underpass, bridges, tall chimneys, dams etc., the cost will go up between 50 – 65 %.
- In case of Special infrastructures like Flyovers, underpass, bridges, tall chimneys, dams etc., the cost will go up between 50 – 65 %.
- Shuttering work should made of cost effective materials, fabrication and labor as far as possible.
- After its usage, immediately shuttering moulds to be carefully released from concrete surfaces and maintenance to be done by cleaning the cement slurry and oiling all surfaces as per specification.
3. Causes of formwork failure :
This failure is happening in the following cases,
- Formwork is not designed for specific purpose, load calculations not dealt accurately.
- Not designed to take horizontal thrust into consideration.
- Adopting improper method of stripping, early stripping and negligence in shore removal. E.g., by removing the free end of cantilever portion first, instead of fixed end of cantilever portion first.
- Inadequate diagonal bracing, and improper packing for vertical props at bottom instead of base plates.
- Due to unable to withstand Vibration forces
- Unstable soil under props and base plates, not maintaining plumb of shoring and giving slant supports.
- Inadequate control of concrete placement over slabs, beams, cantilever (by stacking excess concrete load)
- Lack of attention to formwork details, altering vendor supplied materials.
- Usage of damaged elements likes loosen weld joints for acrospans, broken u clamps, slippery wedges etc.
- Improper vibration and compaction of concrete
4. Safety precaution :
- All Materials used for the erection of shuttering work must satisfy the safety standard and technical specification.
- Always see that, the shuttering work is fixed firmly & properly over a rigid base
- Always note that working area and shuttering work completed area must be protected by means of regular hard barricade,bracing, and additional supports to prevent destruction of shuttering work.
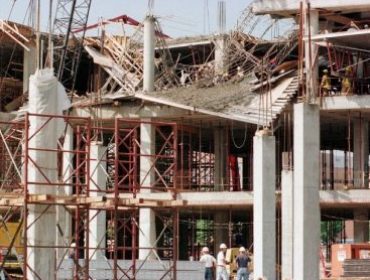
FWF 1
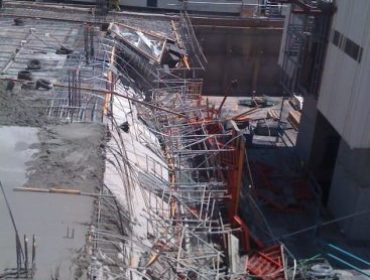
FWF 2
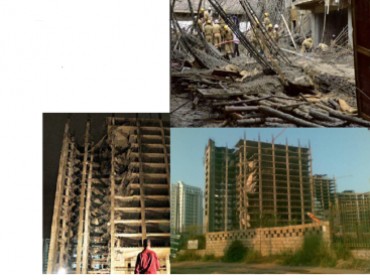
FWF 3
CONTACT US
15/4, gurunath 2 A cross Hanumagirinagar, Chikkallasandra Main Road Subramanyapura,
Bengaluru – 560061
info@myhomemydesign.in
Our Happy Clients
Client Testimonials


LLP, Ex-President- RMC Readymix (India)


MBBS and Chairman at PRANA MEDICAL CENTER, SPECIALIST CENTER FOR DIABETES, ENDOCRINE,
OBESITY. – Kodambakkam – Chennai- 600024
Always Dedicated & Devoted
Latest Projects
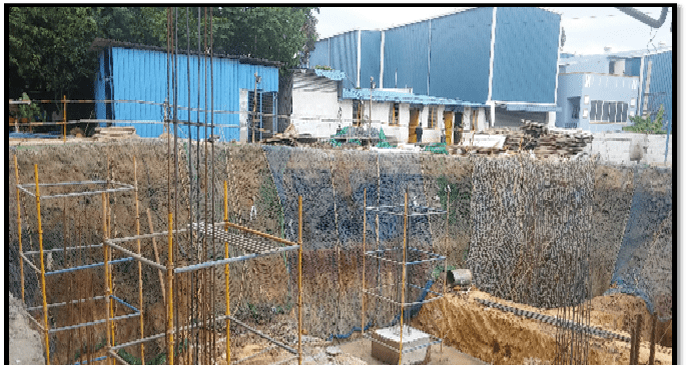
Excavation for basement and footing
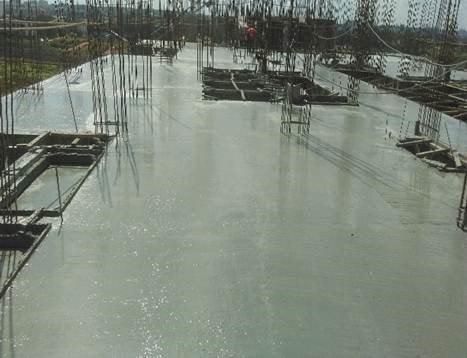
Compaction of Concrete
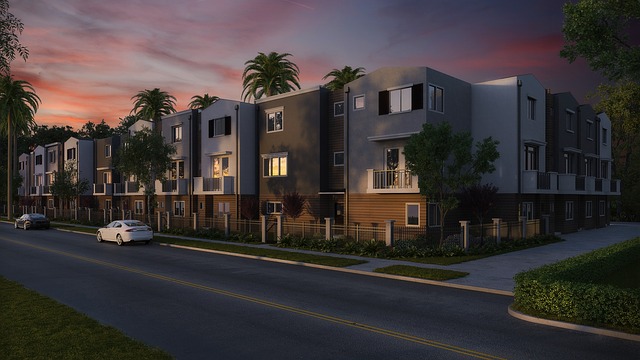
Building ByeLaws for Residential Buildings – All You Wanted to Know
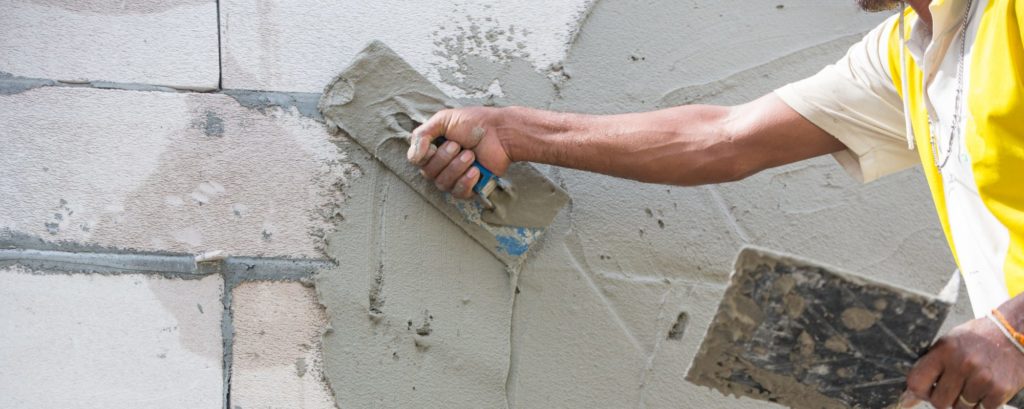
How to Plaster Your House? Guide for Home Plastering
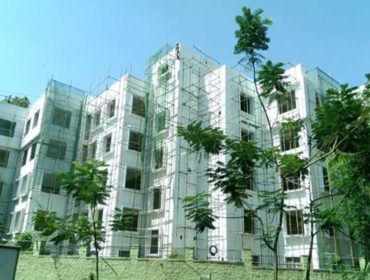
EXTERIOR PAINTS – PAINTING WORKS
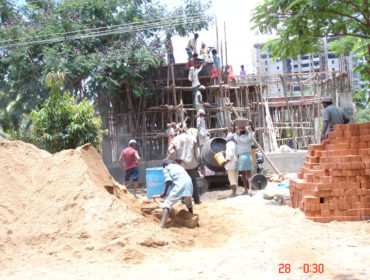