- By Myhome
- July 19, 2019
- 1:06 pm
- One Comment
The following ingredients are necessary for obtaining good concrete in construction field. CEMENT The Cement grade and brand of cement should confirm IS 456: 2000 standards and is recommended by the respective project consultant. Each consignment of cement delivered to the project site must obtain Manufacturers test…
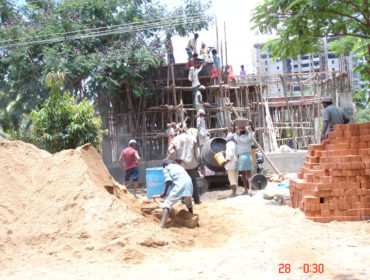
How to Make a Concrete? :
The following ingredients are necessary for obtaining good concrete in construction field.
CEMENT
- The Cement grade and brand of cement should confirm IS 456: 2000 standards and is recommended by the respective project consultant.
- Each consignment of cement delivered to the project site must obtain Manufacturers test certificate (MTC) and is consumed within 1 month of their manufacturing date.
Storing and stacking of cement :
- Storing of cement in a godown should always be in dry, leak proof and as moisture proof as possible and contains minimum number of windows.
- Stack the cement bags on wooden planks or raised solid block platform of at least 150 mm above the floor.
- Cement should be stacked not more than 10 bags in height, and all round clearance of at least 1 meter distance from all walls.
- It has to be well protected during rainy season.
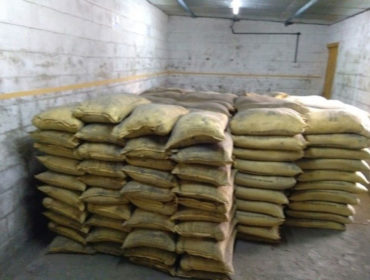
FIG 1
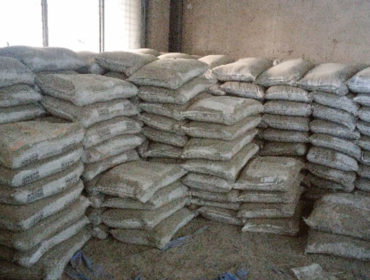
FIG 2
CEMENT STACKING : Fig 1 and 2 : Right way of staking cement at 10 bags height below yellow line
Maintain proper records and see that “first come cement in and first out rule” while issuing cement bags.
Before issuing for work, ensure the cement is tested in-house for consistency, setting time, and strength.
AGGREGATE FOR CONCRETE :
Coarse Aggregates :
- Coarse aggregates confirming to IS 383 and IS 2386 having maximum size of 20 mm and down should be used for all RCC works.
- The aggregate material obtained should be from authorized crushers such as granite, trap and basalt quarry.
- It should be cubical, rounded or angular in shape and free from dust, foreign matter and not thin, porous, laminated or flaky in shape.
Fine Aggregates :
- Fine aggregate meeting IS standards, shall be gritty sand with Fineness Modulus FM ranging between 2.6 to 3.2, silt content should be limited to 5% and there should not be any traces of salt and clay.
- Aggregate having specific gravity less than 2.6 is giving lesser compression strength, and hence not to recommended its usage in concrete.
- If fine aggregate having more dirt, wash sand before use and sand should free from organic matters.
- M Sand : Now a days, there is a scarcity, for availability of good quality of river sand. Many state Governments also imposed ban on sand lifting in river beds, which forces to thinking of an alternative to river sand. As a result, Manufactured Sand (M Sand) is used as substitute for river sand, however, M Sand should confirm IS 383 specifications.
WATER :
- Water used for concrete always should be potable, clean, fresh and free from oil, acid, alkali and organic matter.
- IS 456:2000 gives permissible limits of solids present in water.
- Importance of water for concrete and its test parameters will be explained shortly in upcoming article.
ADMIXTURES :
- Type of admixture and its dosage required for concrete is depends on trial mix done at project site, using available material, and as per design mix by technical consultant.
- Ensure the Shell life of admixture before actually being used at site.
- Stay tuned for : Different types of Admixtures and its uses in future article
Tools required for Concreting :
- Shovels, Trowels, Floating trowel, Masons trowel, Leveling trowels, Line thread, Brushes and buckets, Gum boots, Vibrators, Dumpy level, Spirit levels, Measuring tape, Hammer, Wheelbarrow, Aluminum straightedge (leveler), High pressure water cleaners.
How to make Concrete? Mixing of Concrete : IN-SITU MIXING (Mixing at site)
- Before mixing of concrete, check all necessary stock and storage of materials, tools, equipment and workers including supervisors – all available and present in working area.
- Calibration : Calibration should be done once in every 6 months for weigh batcher, tower crane, builder hoist, compression testing machine (CTM) etc. and these dates should be in force, during its usage for concrete and other works. Affix due date stickers on all equipment for better and easy monitoring.
Concrete mixer :
- Start and run the concrete mixer with one fourth of required water to rotate 3 – 4 times.
- Normally Water required for each load or each bag of cement is between 20 to 25 liters.
- But it is highly advisable to use the water cement ratio as per design mix specification. (between 0.4 to 0.5)
Concrete mixer :
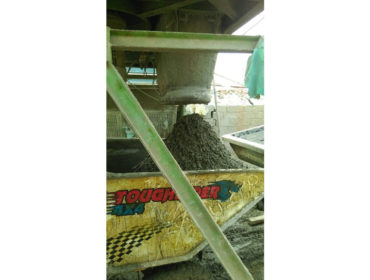
FIG 3: CONTROL ON WATER – CEMENT RATIO
- To controlling moisture content of aggregates is very important and to be checked at frequent intervals, it will vary in rainy and summer seasons.
Loading of concrete into the mixer :
- First, Load the hopper with ½ the coarse aggregate of 20 mm down grade, followed by ½ the fine aggregate of 12 mm down grade.
- Over this, the full quantity of cement should spread.
- Then the final quantity of fine aggregate followed by remaining coarse aggregate to be loaded.
- This type of proper mixing is required to avoid falling of cement while discharging into the drum.
- Finally after loading the drum, the balance quantity of water to be added.
- Mixer drum should be rotated for at least 1 ½ to 2 minutes. The rotation of the drum is to be maintained at 15 to 20 revolutions per minute.
- Note that, if any admixture is used, one liter of water should be kept in reserve.
- Add prescribed dosage of admixture to the water and mix it thoroughly.
- This mixture is poured into the mixer after the drum has rotated for about 90 seconds.
Minimum cement content :
Minimum cement content required per cum of concrete is as per the following below :
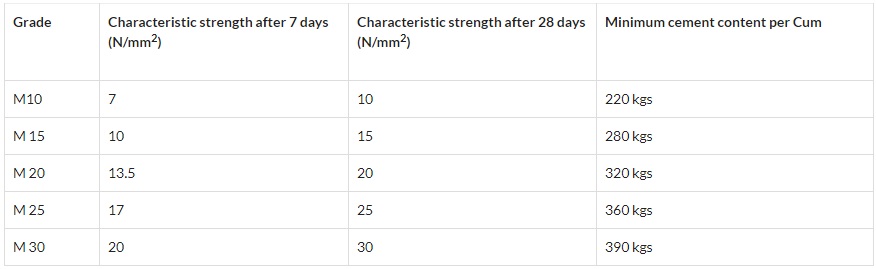
Points to be remember for concreting :
RCC works :
- As Per IS standards, Concrete below M 20 grade should not be used for RCC works.
- See that, Concrete should be reached, placed in position over a good shuttering with steel reinforcement and compacted properly within half an hour of its time of mixing.
- While loading the mixer, follow the design mix criteria for all materials for its correct weight.
- This has to be monitor by deploying experienced supervisor in absence of computerized panel, or for manual loading into the mixer for correct proportion.
Measuring boxes :
- Always use measuring boxes of correct size for loading.
- Use large pans, wheelbarrows, builder hoist o expedite transporting process.
Adsorption :
- Wet the surface of the tools carrier to avoid moisture loss due to adsorption (act as a thin film between tool and concrete)
- Care should be taken in order to avoid segregation and wastage during transportation.
- If segregation occurs, remix the concrete in mixer, before placing.
- Concrete should always made up of well graded aggregate, fluffy and homogenous in colour, if rounded in hands it should form a shape of ball with good consistency.
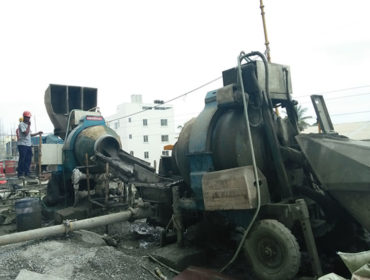
FIG 4 : CONCRETE MIXING IN PROCESS
USING MIXER WITH HOPPER
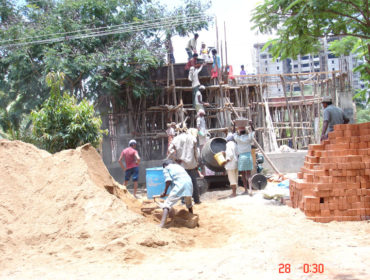
FIG 5 : RESIDENCE ROOF CONCRETING
UNDER PROGRESS
Share on facebook
Facebook
Share on whatsapp
WhatsApp
Share on twitter
Twitter
Share on linkedin
LinkedIn
Share on pinterest
Pinterest
RMC using Batching Plant
If we want go for Ready Mix Concrete (RMC) at project site, many factors are required to be considered, and the same thing will be explained in detail, shortly in coming articles.
Planning:
QC Engineer should plan and decide the required quantity, and order to be placed well in advance, strategy should be worked out in such a way that at least 1 load of 6 cum for every 10 to 15 minutes duration so that concrete is delivered to the site without any hassle.
Checking:
- Before exit transit mixer from project site, Check the empty vehicle for preset concrete in the drum. This will reduces the quantum of concrete received. Check always Concrete should be received with a DC and data cycle sheet clearly showing grade, quantity, water cement ratio, slump measured, and weightage of cement, date and time of manufacturing, quantity of additive added, weight of other ingredients of concrete.
- Caution: Do not accept concrete after lapse of 3 hours’ time from batching plant to project site including complete unloading of concrete. (Check the leaving time of truck from the batching plant in delivery challan).Do not alter the concrete mix by adding additive, water, and cement without prior permission from the QA/QC Engineer.
Slump:
For Pumpable concrete, the Slump recommended for RMC mix is 100 mm to 125 mm and can go up to 150 mm in certain cases.
Concrete Pump, Pipe arrangement and maintenance:
- Concrete pump to be located on horizontal, hard and even surface, to see that easy flow of material to the required place of discharge.
- The horizontal section of pipe should be at least 6 meters before the vertical bend is put.
- The pipe to be reduced to the minimum length, to prevent frictional losses and over pressure exerted on the pump.
- Caution: Always keep in mind that, the pipeline should not be supported on shuttering beam sides, rather it should have its own vertical independent segment. If this is not taken care, the vibrations due to pumping will affect or displace shuttering works causes excessive damages.
- Before supplying actual concrete, always pump rich cement slurry, to lubricate the inner surface of the pipes.
Choking of pump:
- Due to practical problems, or any reason, In case of subsequent supply is not reaching project timely, keep the current transit mixer in running condition, till the next mixer arrives at site. This will avoid choking problem of pipeline, keeping in idle the pump, for long duration.
- Caution: Avoid reverse stroke to clear a choke in pump. The slurry gets flushed out and the problem gets compounded.
- Do not bend the flexible end pipe too much during concreting.
- In unconfined and congested areas, where pipe line is not possible to reach, do not unload directly from the pipe, all shuttering material gets spoiled and alignment may be disturbed. Use Pans and spades and do concrete manually.
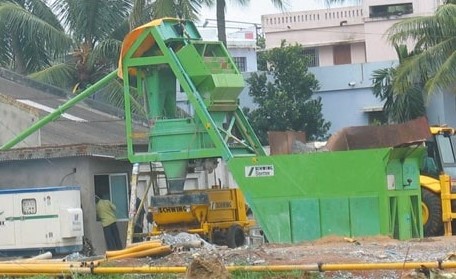
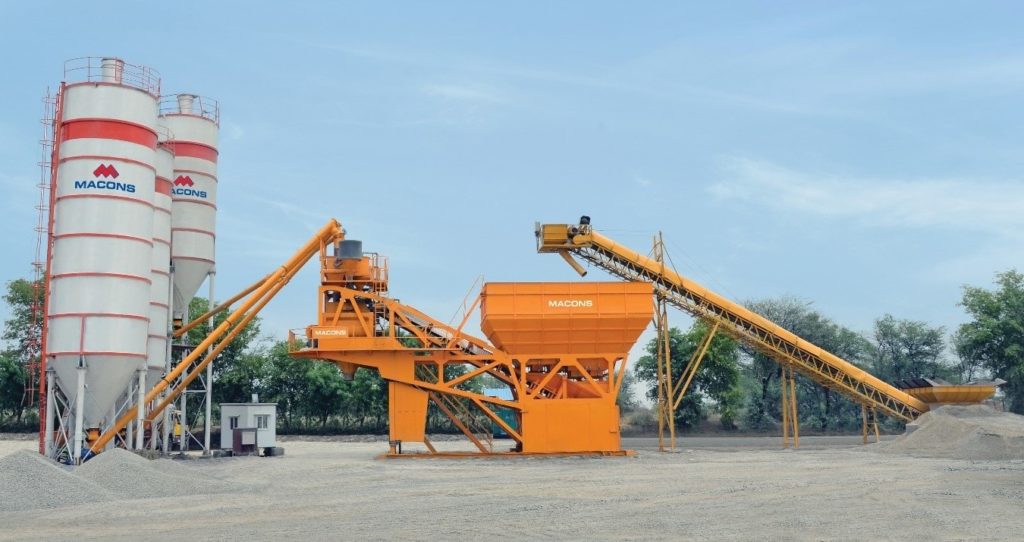
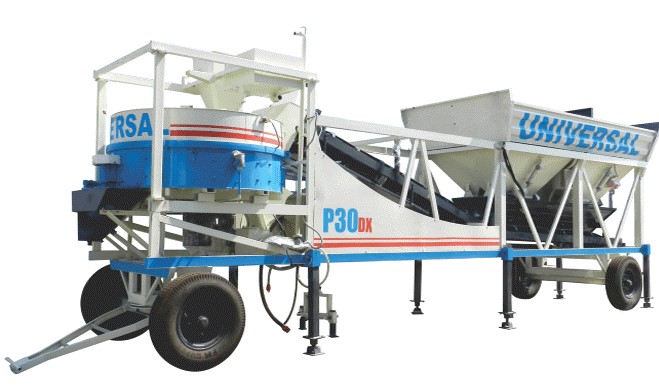
Pingback: itemprop="name">Batching plant - RCC works - (Part 2) - My Home My Design